Titanium CNC Machining
Titanium stands out in the realm of advanced materials, renowned for its exceptional combination of properties that make it highly sought after across diverse industries. Its high strength-to-weight ratio, superior corrosion resistance, and remarkable biocompatibility position it as a material of choice in applications ranging from aerospace components to medical implants.
Titanium is a difficult material to work with which requires the use of precise CNC machining to harness its full potential. Swiss-style machining ensures that the stringent tolerances and exacting specifications required for titanium parts are consistently met. This precision is crucial in industries where the performance and reliability of titanium components are non-negotiable, such as in the aerospace sector, where even the smallest deviation can lead to significant repercussions, or in the medical field, where the biocompatibility of titanium must be preserved without compromising structural integrity.
Incorporating advanced CNC technology such as Swiss Turning in the machining of titanium not only maximizes the material’s inherent advantages but also enhances the efficiency and accuracy of the manufacturing process. This synergy between titanium’s unique material properties and machining precision is what drives innovation and excellence in the production of high-performance titanium parts.
Why Use Titanium?
Titanium is just as strong as steel but is much less dense. This makes it a perfect material for jobs that require great strength but are limited by the weight of the part. Titanium also differs from steel in its corrosion resistance, which is why it has many applications in naval applications such as ships and submarines.
Titanium also boasts great resistance to temperature, both high and low. This, combined with its lightweight characteristics, makes it the perfect metal for the aerospace industry. Biocompatibility is another critical attribute of titanium, making it highly suitable for medical applications. Titanium is non-toxic and not rejected by the human body, which means it can be safely used for implants, prosthetics, and surgical instruments. Its ability to integrate with bone tissue without causing adverse reactions ensures long-term success in medical procedures.
Titanium CNC Machining Capabilities
At McCormick Industries, our expertise in titanium CNC machining is unparalleled, particularly through our use of advanced Swiss turning machines. These precision instruments allow us to achieve tolerances as low as +/- .0001 inches, ensuring exceptional accuracy and consistency in every part we produce. We specialize in working with various grades of titanium, each selected to meet the specific requirements of your project, whether it be for aerospace, medical, or industrial applications. Our commitment to quality is evident in our meticulous machining processes and rigorous quality control measures, making McCormick Industries a trusted partner for all your high-precision titanium machining needs.
McCormick Industries: Experts In Quality CNC Machining for Titanium
With over 25 years of experience in Swiss-style machining and a fleet of 10 advanced tuning centers, McCormick Industries stands at the forefront of titanium CNC machining. Our state-of-the-art equipment, coupled with the unparalleled skill of our machinists, ensures that each project meets the highest standards of quality and precision.
Our commitment to excellence is evident in our meticulous quality control processes. From the initial design phase to the final inspection, every step is monitored and refined to guarantee superior results. Trust McCormick Industries for your titanium CNC machining needs, and experience the difference that expertise and dedication can make.
Common Applications For Titanium CNC Machined/Swiss Machined Parts
When it comes to the medical industry, the use of titanium in implants is nothing short of revolutionary. Titanium’s unique properties make it the material of choice for a wide range of medical applications, from joint replacements and dental implants to surgical instruments. The foremost reason for this preference is biocompatibility. Our bodies tolerate titanium exceptionally well, which means there’s a significantly lower risk of rejection or adverse reactions. This is crucial for something as invasive as a hip replacement or a dental implant, where the material will be in direct contact with body tissues and fluids for an extended period.
See Also: Aluminum Medical Machining
Precision is another critical factor. CNC machining and Swiss precision machining technologies allow for the production of components with incredibly tight tolerances. In the medical field, even the slightest deviation can be the difference between success and failure. For instance, a joint replacement must fit perfectly to ensure proper movement and reduce wear over time. The accuracy provided by these advanced machining techniques ensures that each component meets the stringent requirements necessary for medical applications, ultimately contributing to better patient outcomes.
In the aerospace sector, the quest for materials that are both lightweight and strong is never-ending. Titanium brilliantly fits this bill. Its high strength-to-weight ratio makes it an ideal choice for a variety of aerospace components, including aircraft engines, airframes, and fasteners. The reduced weight helps improve fuel efficiency and performance, while its strength ensures the structural integrity of critical parts under extreme conditions.
Moreover, the aerospace industry has some of the most stringent quality requirements of any sector. Components must be able to withstand extreme temperatures, pressures, and mechanical stresses without failing. The precision capabilities of CNC machining and Swiss precision machining are essential here, allowing for the creation of parts that meet these rigorous standards. Each component must be flawless, as even a minor defect could lead to catastrophic failure. By employing these advanced machining techniques, manufacturers can produce reliable, high-quality parts that contribute to the safety and efficiency of modern aircraft.
In military applications, the durability and corrosion resistance of titanium make it an invaluable material. Whether it’s used in armored vehicles, naval vessels, or aircraft components, titanium’s robustness ensures that equipment can withstand the harshest conditions. Military gear often faces extreme environments, from saltwater exposure to high-impact situations, and titanium’s resistance to corrosion and wear makes it ideally suited for such demanding applications.
Furthermore, the reliability of military equipment can be a matter of life and death. The precision offered by CNC machining and Swiss precision machining ensures that each part meets the exacting standards required by military specifications. Whether it’s a component in an armored vehicle or a fastener in an aircraft, the part must perform flawlessly under pressure. The advanced machining techniques used to produce these components ensure that they meet the highest standards of durability and reliability, providing the assurance needed in critical military operations.
Titanium Swiss Machined Parts from McCormick Industries
At McCormick Industries, we are proud to offer precision titanium machining services. Our extensive knowledge and experience in manufacturing titanium parts allow us to deliver quality parts with tight tolerances. To learn more about our titanium machining services, submit your inquiry using the form below:
"*" indicates required fields
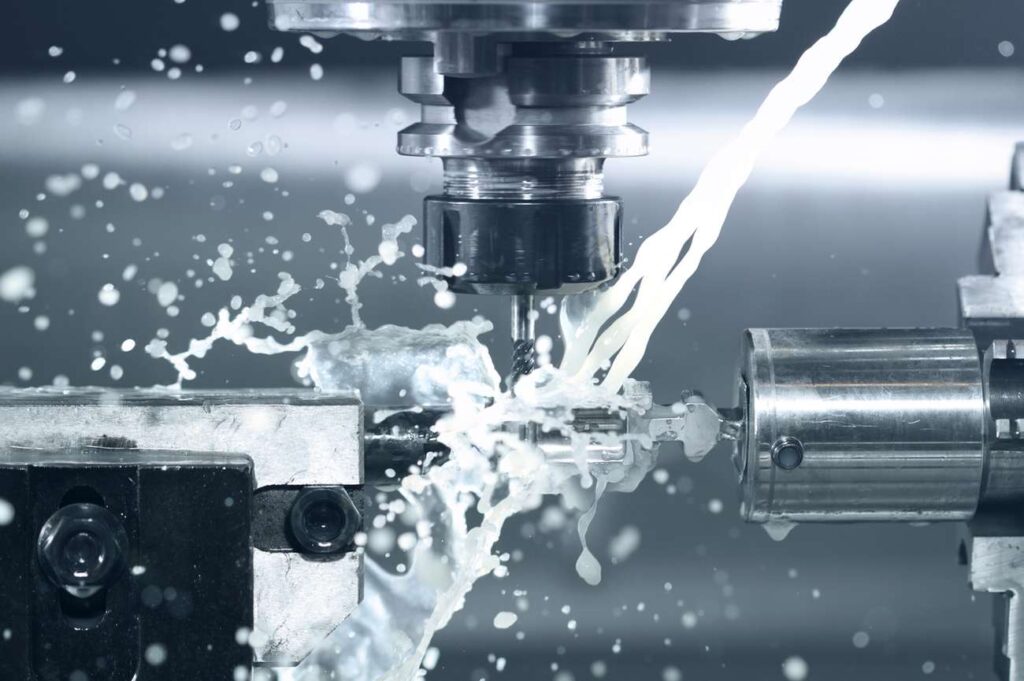